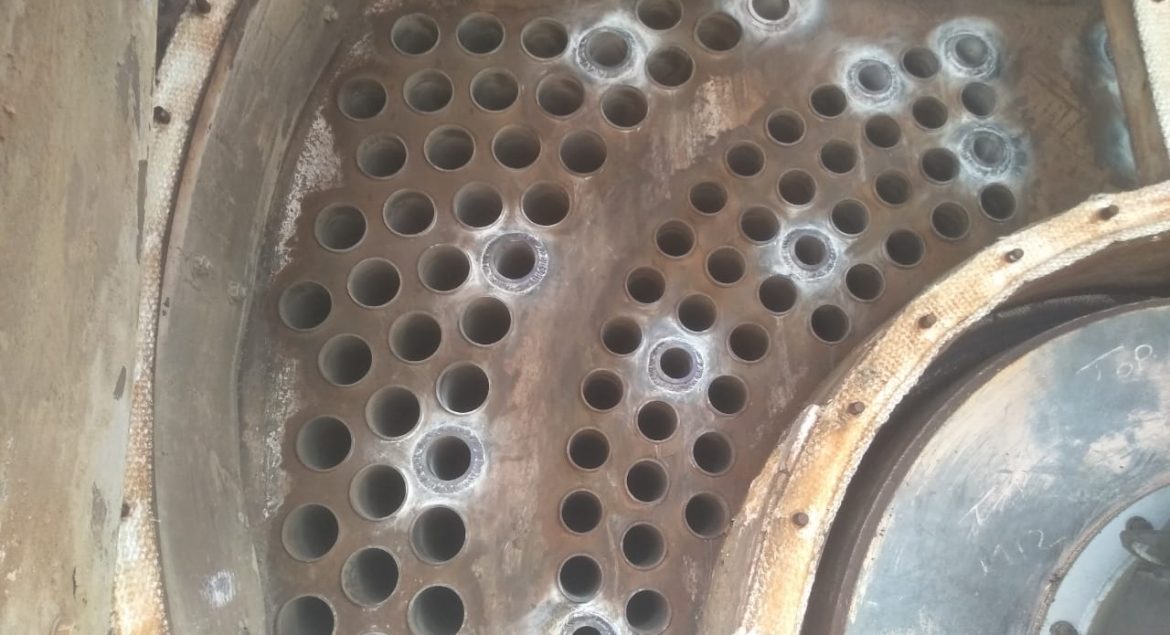
BDNDT Provide Ultrasonic Thickness Testing Service on Boiler tubes to ensure the safety in Bangladesh.
Boiler tubes play a critical role in the operation of boilers, serving as conduits for the flow of water and steam in a boiler system. This application note explores how to measure the thickness of steam boiler tubes using Ultrasonic Thickness Gauge. Their primary functions include facilitating the transfer of heat from the combustion process to the water, and subsequently, to generate steam. Boiler tubes are subject to stringent safety standards to ensure the safe operation of boilers.
Importance for Measuring the Thickness of Boiler Tubes
The very high temperatures found inside steam boilers (in excess of 800 degrees Celsius or 1472 degrees Fahrenheit) can cause the formation of a specific type of hard, brittle iron oxide called magnetite on the inside and outside surfaces of steel boiler tubing. The presence of this oxide layer on the outside of tubes can interfere with ultrasonic wall thickness measurements using common dual element transducers for two reasons: it can have a very rough surface that prevents proper sound coupling, and the oxide thickness is added to the steel thickness.
However, as its name implies, magnetite is magnetic, and that property permits the use of magneto strictive electromagnetic acoustic transducers, such as the E110-SB. EMATs offer several advantages over conventional dual element piezoelectric transducers: the need to remove oxide scale is eliminated, the scale thickness is not added into the wall thickness measurement, and measurements can be made quickly and without the need for liquid couplant.
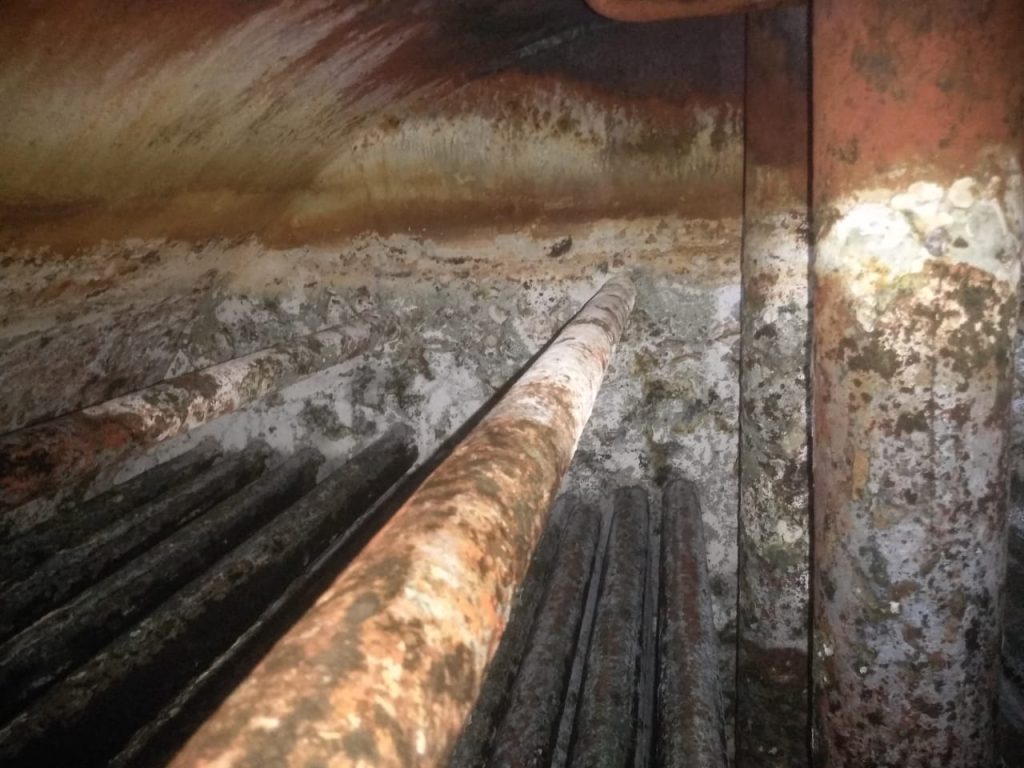
Ultrasonic Thickness Testing Process:
Preparation: Ensure that the boiler is safely shut down, cooled, and depressurized to allow for inspection. Clean the external surface of the boiler tubes to remove any debris, scale, or corrosion products that could affect the accuracy of measurements.
Selection of Equipment:Choose appropriate ultrasonic testing equipment based on the specific requirements of the inspection. This includes selecting the right ultrasonic transducer, couplant, and thickness gauge.
Calibration: Calibrate the ultrasonic testing equipment using a reference standard with a known thickness. Calibration ensures the accuracy of thickness measurements.
Coupling: Apply a suitable couplant (ultrasonic gel or water) on the surface of the boiler tube. This ensures proper acoustic coupling between the transducer and the tube, allowing sound waves to travel through the material
Transducer Placement: Place the ultrasonic transducer on the external surface of the boiler tube at the location where thickness measurements are required. The transducer emits ultrasonic pulses into the tube wall.
Ultrasonic Pulse: Send ultrasonic pulses through the tube wall. The sound waves travel through the material until they encounter the opposite side of the tube wall, where they are reflected back to the transducer.
Thickness Measurement: Measure the time taken for the ultrasonic waves to travel through the tube wall and return to the transducer. The thickness of the material is directly proportional to the time delay of the reflected waves.
Data Analysis: Analyze the ultrasonic test data to determine the thickness of the boiler tube wall. Compare the measured thickness with the baseline thickness (initial thickness) to identify areas of corrosion or thinning.
Recording and Reporting: Record the thickness measurements at various locations along the length of the boiler tubes. Generate a comprehensive report that summarizes the condition of the tubes, highlighting areas where corrosion or thinning has been detected.